WEDEL/EISENDORF: “Jeg tror bare, jeg tager brillerne af allerede nu”
Allerede før man træder ind i hallen, er fugtigheden massiv. Xellas projektleder Jens Rønsholt tager derfor sine forbehold, før han åbner døren og går ind.
Døren åbnes, den nærmest tropiske varme rammer. Åndedrætsbesværet sætter ind.
Det er som at stikke hovedet ind i en ovn. Og det er faktisk præcis, hvad det er. Det er i det rum, hvor porebeton genanvendes og bliver til nye elementer.
Sukker, mel, gær
Eurodan-huse er de første i Danmark til systematisk at gå sammen med leverandøren Xella om at sende deres rester af porebeton til den tyske fabrik i Hamborg-forstaden Wedel. Når det når fabrikken, bliver det smidt i en knuser. Herefter bliver det knuste beton enten kørt videre og genbrugt som for eksempel kattegrus. Ellers kommer det ned i noget, der mest af alt bare er en gigantisk kageform.
Og det er her, det førnævnte rum kommer i spil.
Sand, kalk, vand, porebeton og en lille smule cement som bindemiddel mikses sammen, og til sidst kommes der aluminiumspulver ned i – kagens gær. Det får, sammen med den førnævnte luftfugtighed, den nye porebetonblanding til at hæve – akkurat som man kender det fra køkkenet derhjemme.
Hvis ikke fugtigheden er god nok i rummet, klasker kagen sammen – akkurat som nogen kender det fra køkkenet.
– Vi konkurrerer mod beton, og her er det her produkt noget mere bæredygtigt. Alt, pånær den genbrugte porebeton og lidt cement, er naturens egne materialer, og cementen bruges mest til at binde hele blandingen sammen, siger Lars Nygaard, der er salgsdirektør hos Xella Danmark.
Efter hævningen bliver porebetonskagen smidt i ovnen, skåret fra hinanden og videre ind i en autoklave, hvor 200 grader og et tryk på seks-syv bar producerer et nyt element.
Med eller uden cement
Men hele processen kan også stoppes allerede efter knusningen, hvor det kan køres videre til Eisendorf. En by, cirka 50 kilometer fra den dansk/tyske grænse. Her bliver porebetonen også genanvendt, men på en lidt mere traditionel metode.
I stedet for at finde byggebranchens svar på bagepulver, gær og mel, bliver elementerne her først presset, før de bliver brændt i en autoklave. Og modsat Wedel-fabrikken er det udelukkende kalk, sand, porebeton og eventuelt vand, der blandes sammen.
– Det er svært at sige, hvilken en af de metoder, der er den mest bæredygtige. Fra fabrikken i Wedel har man jo en smule cement i, men til gengæld er det et noget lettere produkt. Kalk/sand-stenen er helt uden cement, men det er også noget tungere, så man kan ikke fragte så meget af det ad gangen. Men begge dele er noget mere miljørigtigt end klassisk beton, siger Lars Nygaard.
I Eisendorf er fabrikken meget automatiseret. Her er der kun 18 mennesker ansat i en virksomhed, der kører døgnet rundt. I alt producerer de elementer til cirka 15 huse om dagen.
Ny trend
Xella ejer begge fabrikker. Cirka 60 procent af den samlede element-produktion i Wedel-fabrikken ender da også i Danmark.
– Det virker som om, at der er ved at blive skabt en trend, for tidligere har der ikke rigtig været dansk interesse for den måde, produktionen er foregået på. Så vi håber også, at der kommer et større fokus på bæredygtighed, når nu Eurodan er begyndt på det, siger Lars Nygaard.
Udover porebetonen genbruger Eurodan også deres Rockwool i en lignende aftale.
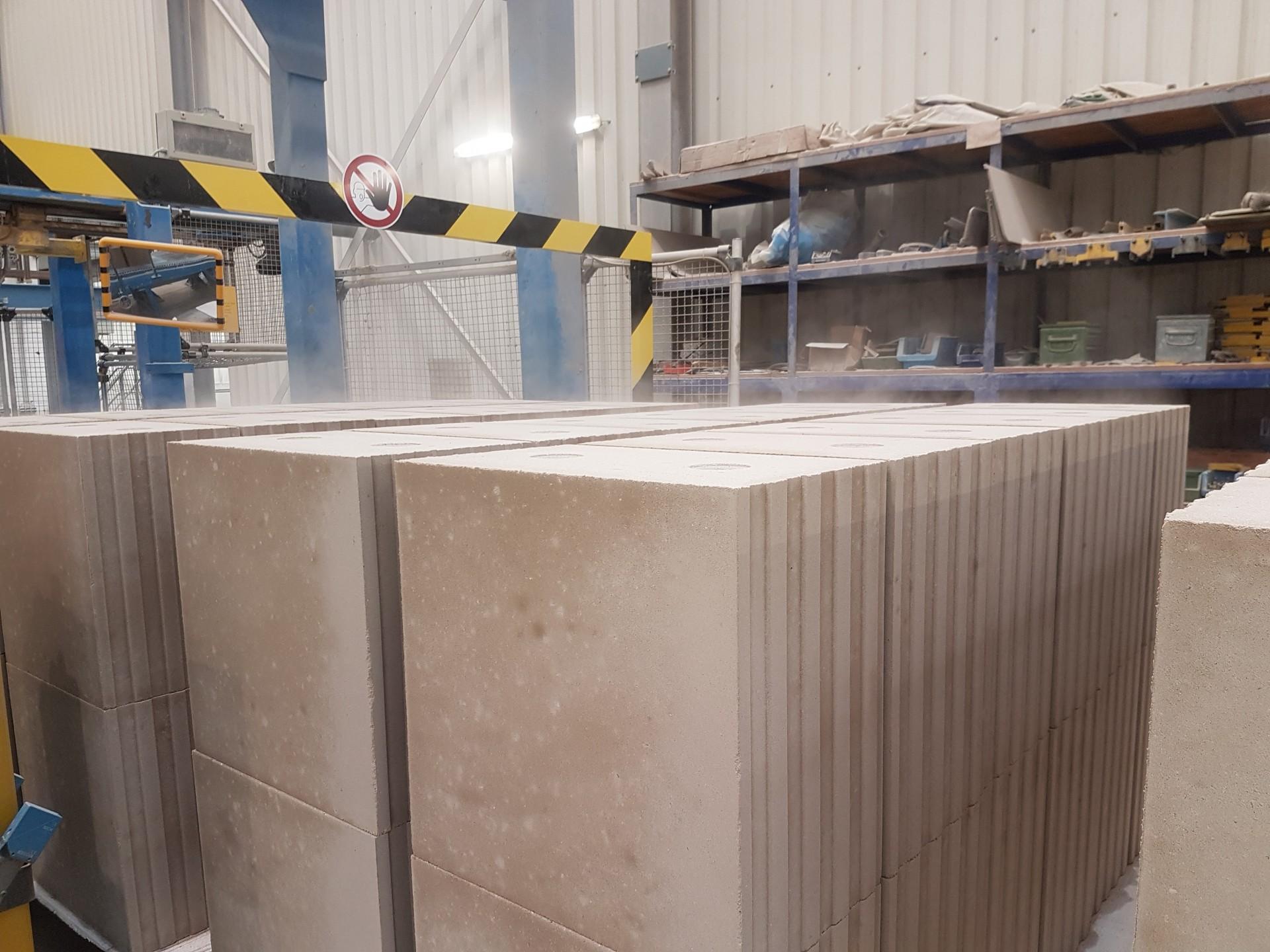
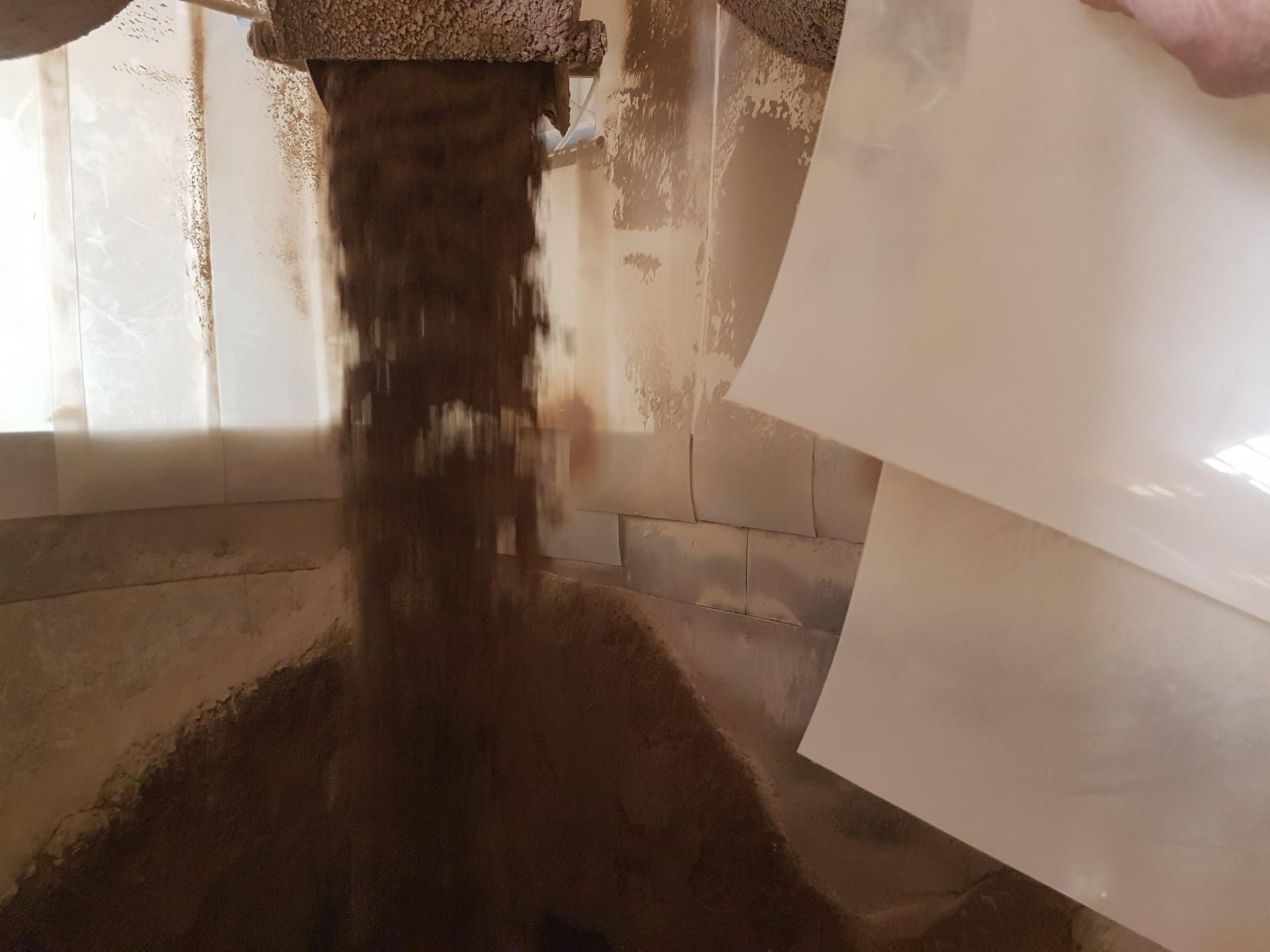