Bæredygtighedstanken siver stille og roligt ind i alle revner og sprækker i byggebranchen. Også i betonbranchen, hvor man over årene ofte er blevet skældt ud for sit høje CO2-aftryk. Nu myldrer det imidlertid frem med tiltag, hvor man både materiale- og procesmæssigt gør en stor indsats for fremadrettet at sænke aftrykket således, at beton fortsat er et realistisk byggemateriale at arbejde med. Også efter sommeren 2025, hvor skærpede LCA-krav træder i kraft.
Det er blandt andet tilfældet hos IBF, Ikast Betonvare Fabrik, der er en af Danmarks største leverandører af fabriksbeton og diverse løsninger til belægning og afløb samt tagsten og murværk. Her har man for nylig udgivet sin første ESG-rapport (Environment, Social and Governance), og ifølge administrerende direktør Stefan Schmidt Clausen markerer den et stort spring fremad, når det gælder bæredygtighedstanken hos IBF.
ESG er nu en strategisk indsats
Fra at være en tilbageholdende virksomhed, der har holdt kortene tæt til kroppen, vælger man efter eget udsagn nu en strategi, hvor man spiller med åbne kort. Den nye kurs viser således, at bæredygtighed er en af topprioriteterne i IBF’s strategi, og nu har man sat alle sejl til med henblik på at nå en 70 % CO2-reduktion i 2030.
– IBF indså allerede for flere år siden, at innovation og bæredygtighed er vigtige parametre i fremtidens betonbranche. Derfor har vi i lang tid arbejdet med at udvikle recepter med mindre cement, og drypvist har vi bragt nye produkter på markedet, som er fremstillet med væsentligt mindre CO2-udledning end tidligere. Det er bare ikke noget, vi har talt så meget om. Den jyske beskedenhed fornægter sig ikke, forklarer administrerende direktør Stefan Smidt Clausen med et smil.
Udviklingen startede sidste år i 2023, da man valgte at etablere en egentlig ESG-afdeling med det formål at gøre bæredygtighed til en af topprioriteterne i virksomhedens fremtidige strategi. Det er det arbejde, der altså nu har ført til udgivelse af koncernens første ESG-rapport. I denne offentliggør IBF for første gang virksomhedens vision og mission samt, hvorledes bæredygtighed er koblet til disse.
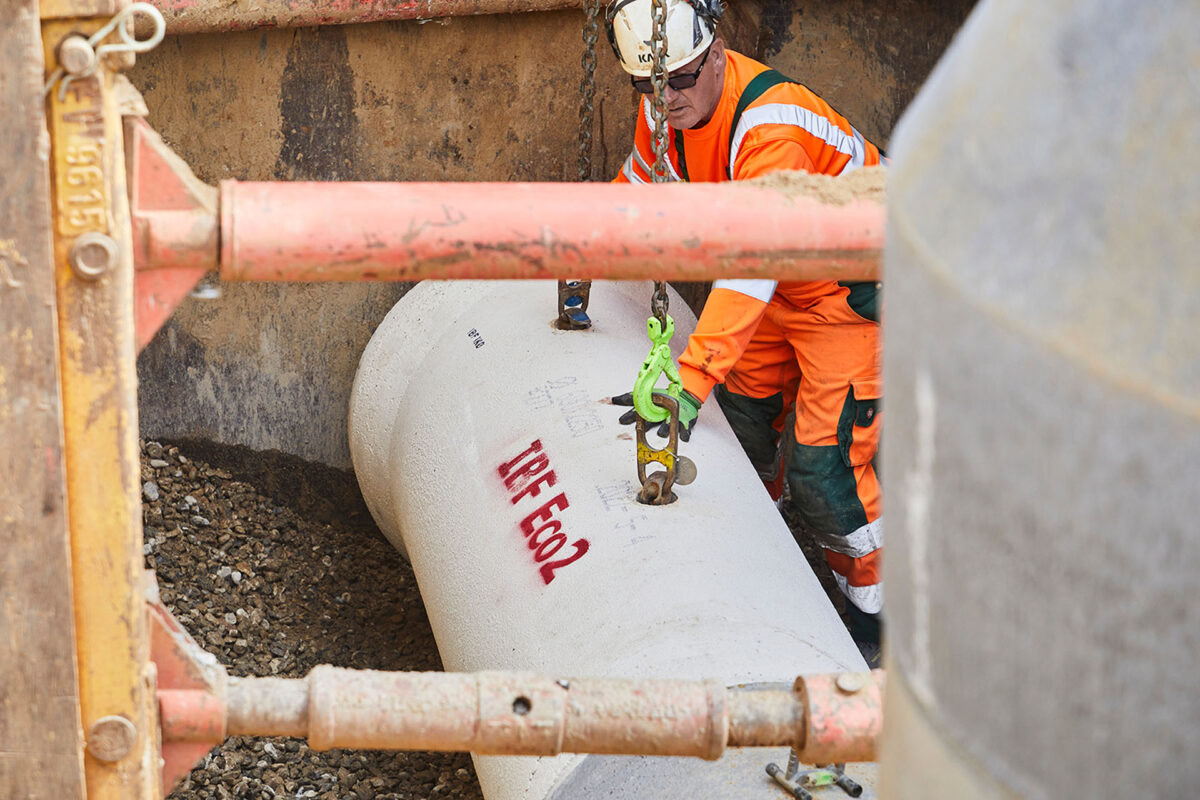
Fliser der gror helt af sig selv
En af de helt store nyheder i rapporten er, at man arbejder på i 17 sideløbende udviklingsprojekter, der alle sammen handler om at nedbringe CO2-udledningen fra beton. Et af projekterne er en millionsatsning, hvor målet er at blive i stand til at dyrke beton ud af mikroorganismer. Lidt som et koralrev, men her foregår det blot i en produktionshal, og slutproduktet er fliser.
Andre projekter er knapt så eksotiske, men potentialet er mindst lige så stort. I IBF’s optik handler det nemlig om i samarbejde med forskningsinstitutioner og andre betonproducenter at finde fremtidens betonrecepter ved hjælp af cirkulær økonomi og genbrug af restmaterialer.
– De mange eksempler på lovende produkter og projekter i rapporten viser, at der ér håb for beton. Endda et stort håb. Derfor tør jeg godt sige, at IBF ikke længere vil nøjes med at levere beton til tiden, som firmaets slogan lyder. Vi vil også levere beton til fremtiden, siger Stefan Smidt Clausen videre.
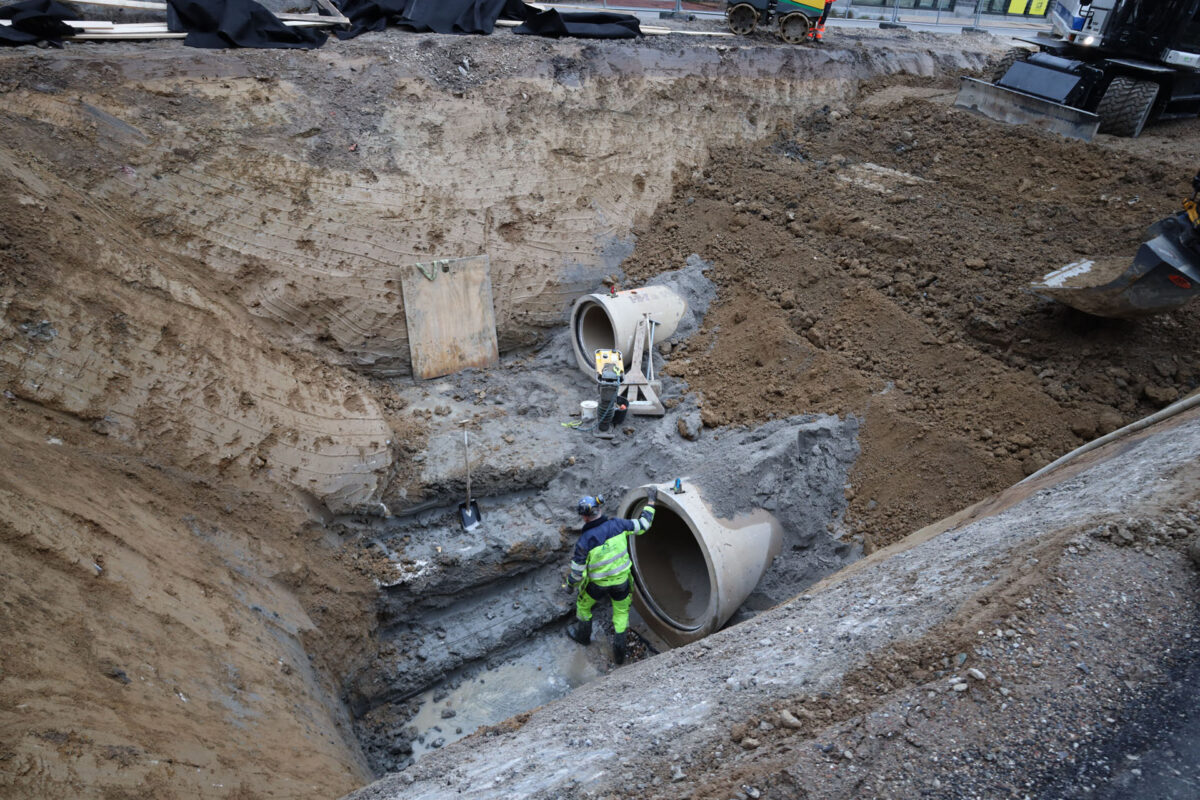
Slagger i stedte for flyveaske
Hos Industri Beton, der er en del af IBF-koncernen, kigger man også i en mere bæredygtig retning. Her producerer man blandt andet betonelementer til byggeriet samt til anlæg og infrastruktur, og ESG-indsatsen tæller naturligvis ligeledes i aktiviteterne her. Således har Industri Beton en bred palet af recepter, som medfører, at man kan optimere CO2-udledningen i forbindelse med opførelse af fremtidens bygninger.
I årevis har betonindustrien anvendt flyveaske som fyldstof i forbindelse med produktion af beton. Årsagen har været et ønske om at mindske cementindholdet med det formål at reducere betonens CO2-aftryk, men flyveaske, der er et overskudsprodukt fra de kulfyrede kraftværker, er ved at være en mangelvare i takt med, at der satses mindre på kul. Tilgængeligheden bliver med andre ord mindre.
I stedet har man, i samarbejde med IBF, arbejdet med formalet, granuleret højovnsslagge, der er et restprodukt fra stålindustrien. Det kan lyde nyt og spændende, men i virkeligheden er der tale om velkendt teknologi. Blandt andet i Tyskland har man i årevis anvendt, Ground Granulated Blast-furnace Slag (GGBS), som den officielle betegnelse er.
Hvad er GGBS?
GGBS (Ground Granulated Blast-furnace Slag) er betegnelsen for formalet, granuleret højovnsslagge fra stålindustrien. Det er et restprodukt fra produktionen af stål, og det kan anvendes som erstatning for cement i betonelementproduktionen. CO2-udledningen fra GGBS er væsentligt lavere end cement, fordi de gældende regler for CO2-beregninger altid tilskriver hele CO2-udledningen fra produktionen af et produkt til selve hovedproduktet, i dette tilfælde stål. Når GGBS erstatter cement i betonelementproduktionen, reduceres CO2-udledningen simultant med mængden af cement.
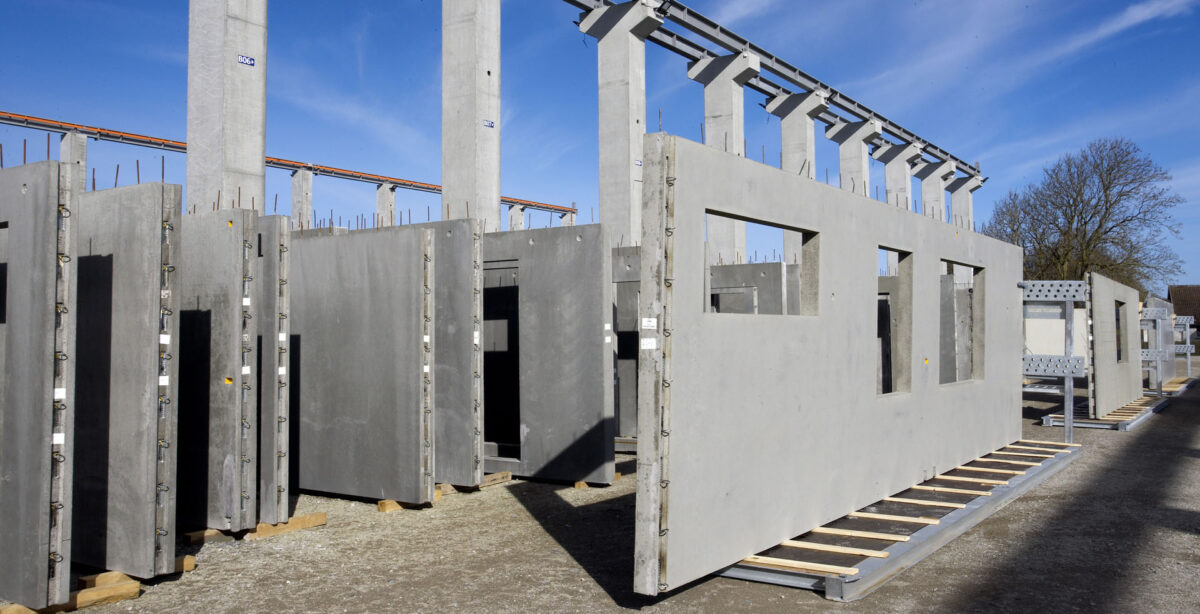
EPD’er øger gennemsigtigheden
Det har resulteret i et standard afløbssortiment fra IBF med en CO2-reduktion på cirka 40 % alt efter produkt, men ofte kan der være tale om en væsentlig større reduktion. Desuden er der tale om betonelementer fra Industri Beton, hvor CO2-udledningen reduceres med op til 43 %.
Industri Beton har nu mulighed for at skabe projektspecifikke EPD’er, der bliver udarbejdet direkte til det enkelte byggeprojekt. Derved bliver datagrundlaget og resultatet af miljøbelastningen udregnet præcist. De projektspecifikke EPD’er er en vigtig grundsten for at opnå og kunne dokumentere det optimerede klimaaftryk i det enkelte byggeprojekt.
– Baggrunden for de projektspecifikke EPD’er ligger i vores produkt-EPD på en 200 mm massiv væg, som er baseret på et års produktion af vægelementer. En projektspecifik EPD øger gennemsigtigheden, så betonelementernes miljøpåvirkning er synliggjort, når bygherre og entreprenør skal vurdere miljøbelastningen ved opførelse af nye byggeprojekter og udarbejdelse af klimaregnskaber, forklarer Carsten Greibe, der er ansvarlig for Quality, Health, Safety and Environment i Industri Beton.